UV LED & PHOTOPOLYMER TECHNOLOGY
Who's ready for some technical talk?! I hope you have your flexo dictionary handy...
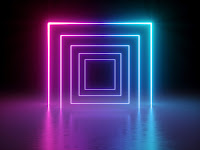
UV LED Advantages
At this point, we need to take a step back into the “so what” question – why are we even interested in UV LED curing to begin with? The answers relative to flexographic platemaking are short and simple:
2) Automation
As a result, photopolymer formulations that were developed with broad band bulbs in mind can quite possibly behave differently, and unpredictably with these new systems despite their wavelength target similarities. To date, there are many formulations that have become “qualified” in these systems, so it’s safe to say we, as the plate developers, have had a bit of serendipity with respect to the interactions between plates and light sources. There are, however, things that we have learned about along the way that will help guide us on where to go next.
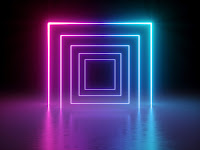
As photopolymer plate formulators, manufacturers and suppliers, we often get asked about emerging technologies and their impact on flexographic printing plate development. Sustainability, printed electronics, 3D Printing are just a few “buzzwords” we hear a lot about, BUT…UV LED technology may be the most “emerged” technology that we come across today. We’d like to take a few minutes to discuss how we, from the plate development and supply side of the fence, see this technology playing out and where we see ourselves standing in this growing field.
UV LED Technology in Flexo Platemaking
UV LED Technology in Flexo Platemaking
While the most common application of UV LED in flexographic printing today is often seen as the “on press” or print application area, the use of UV LED for curing flexographic plates has been around for longer than one may think. The use of UV LEDs has been most successfully applied via Esko in their “Inline” technology that combined plate ablation systems with UV LED curing technology - in this case, the plate could be ablated and cured on the same unit. While the combination brought about an advancement in equipment consolidation, along with solid print performance that was sustained over a period of years, a separate back exposure step was still required and the additional curing step resulted in a productivity bottleneck in this technology.
An additional application surfaced within the last few years, in which UV LED light sources were used in concert with standard fluorescent bulks to produce a “flat-top dot” printing plate without the need for tying up your imager…GAMER CHANGER! The UV LEDs main function, in this case, were to “outrun” oxygen during the curing step, allowing for the formation of a flat dot surface, while the fluorescent bulbs completed the bulk curing process in the printing plate. While it did isolate the curing step back to a separate exposure frame and away from the imager, a modified exposure unit was required, along with the need for multiple curing steps- thus, the productivity and expense of such a unit may not have been ideal for certain segments of the market. With productivity at the top of everyone’s minds these days, we knew this was not going to be the end game.
The most recent addition to UV LED curing is a full LED-based, standalone exposure system. Several of these have been publicized within the past 2-3 years, with one system receiving dominant praise in the industry to date, drumroll please…the Esko XPS Crystal system. This system allows for simultaneous, UV-LED based curing on the back and front side of the printing plate, in a manner that is consistent in its application pass to pass, and plate to plate. This technology has also allowed for the introduction of a “platform” approach to platemaking automation, in which ablation to exposure, or further into plate processing - can be aligned together within a one, single production system…now that’s what we were waiting for.
Eskso XPS Cyrstal in our Atlanta Innovation Center |
UV LED Advantages
At this point, we need to take a step back into the “so what” question – why are we even interested in UV LED curing to begin with? The answers relative to flexographic platemaking are short and simple:
1) Consistency
Photopolymers are not moody nor highly intelligent autonomous creatures. They are a mixture of chemicals designed with a class of behaviors and performance characteristics in mind, targeting a finished print application. Some could refer to them as high maintenance, as they require many other technologies to be successful- exposure, washout, on press components, etc. Any variation of these components can lead to variation in the application of said photopolymer materials, and this includes plate exposure technology. The more widely variable the exposure technology, the more variation one can expect from your photopolymer plate, seems logical enough. This is where UV LED technology holds a distinct advantage- an unparalleled uniformity of light intensity across the width of the exposure device, which translates into more uniformity of the finished printing plate itself. More uniformity means more consistency, and more consistency lends itself to more repeatable and predictable finished results. This, was the missing piece our industry was looking for all along.
There are additional areas of benefit relative to how UV curing is applied to the printing plate. In addition to supplying consistent and predictable amounts of UV energy to the plate, applying this in a consistent manner is also important. The ability to cure each plate the same way- meaning no differences relative to temperature, energy or even the time between the front side and back side exposures- lead to greater and greater consistency. And with consistency, comes standardization and predictability…and ultimately, SUCCESS!
UV LEDs are extremely powerful for their size, but it’s the size itself that brings the most flexibility into the platemaking arena. UV LEDs are most aptly integrated into smaller arrays that can be applied as a “light bar” for platemaking in which the bar itself, or the plate, moves under the irradiation source. This allows for a streamlined design, albeit one that is still highly, highly complex in its application despite the simplicity of the appearance.
This streamlined approach has enabled several integrations of UV LED designs to date. One such integration is the “connection” of ablation to exposure, wherein the plate is automatically transferred from one unit to the other. Additionally, several examples of exposure to processor integrations have been implemented and currently can be found within the industry today, but have been limited to solvent processing only.
The ultimate consolidation is the full combination: ablation - exposure - processing. How well can thermal or water wash systems integrate into this technology of the future? We’ll have to wait and see.
3) Future considerations
While the automation function is certainly a “future consideration” when evaluating UV LED technology, the other areas of consideration are related to productivity and environmental considerations. Productivity and sustainability - this won't be the last time you hear about this.
For productivity purposes, we merely point to the expanding trends of “inherently flat top” formulations that have integrated into the market within the past few years, which was pioneered by, ahem…MacDermid. These formulations have changed the way we view formulation possibilities, and have increased the platemaking speed and efficiency as a result. Therefore, our “new normal” has changed - speed is here, and UV LED can help to enhance the control of these types of formulations during platemaking even further.
For productivity purposes, we merely point to the expanding trends of “inherently flat top” formulations that have integrated into the market within the past few years, which was pioneered by, ahem…MacDermid. These formulations have changed the way we view formulation possibilities, and have increased the platemaking speed and efficiency as a result. Therefore, our “new normal” has changed - speed is here, and UV LED can help to enhance the control of these types of formulations during platemaking even further.
Additionally, a long-term consideration of UV LEDs when compared to existing fluorescent systems is the...c’mon you know the answer…environmental aspect and the elimination of mercury-based components. While not an active element in regulations today for flexographic platemaking systems, the regulations have slowly started to evolve in the areas of household lights, and the elimination of incandescent lighting within some regions. There will come a time in which mercury-based light sources may well be highly regulated or even banned in the future, and we as an industry must prepare for that eventuality.
Photopolymer Interaction
Now that the stage has been set for the importance of UV LED technology and its growing impact, how do we as formulators deal with this technology? The ink formulators have borne the brunt of this emergence thus far - being forced to contend with reformulation efforts, new raw materials, functional differences, etc. On the platemaking side, there are essentially two possibilities we are forced to face: how do our current formulations interact with UV LED curing systems, and how do we modify or develop new formulations that take advantage of these light sources? Let’s discuss…
Now that the stage has been set for the importance of UV LED technology and its growing impact, how do we as formulators deal with this technology? The ink formulators have borne the brunt of this emergence thus far - being forced to contend with reformulation efforts, new raw materials, functional differences, etc. On the platemaking side, there are essentially two possibilities we are forced to face: how do our current formulations interact with UV LED curing systems, and how do we modify or develop new formulations that take advantage of these light sources? Let’s discuss…
SPOILER ALERT - it's about to get technical...
While the existing UV LED platemaking systems do target the same peak wavelength for curing (365 nm) UV LEDs are inherently near-monochromatic (See Figure 1), i.e. a very narrow wavelength distribution, when compared to fluorescent bulbs (See Figure 2).
While the existing UV LED platemaking systems do target the same peak wavelength for curing (365 nm) UV LEDs are inherently near-monochromatic (See Figure 1), i.e. a very narrow wavelength distribution, when compared to fluorescent bulbs (See Figure 2).
![]() |
Figure 1: Spectral Output of LED Exposure Unit |
![]() |
Figure 2: Spectral Output of Fluorescent Exposure Unit |
As a result, photopolymer formulations that were developed with broad band bulbs in mind can quite possibly behave differently, and unpredictably with these new systems despite their wavelength target similarities. To date, there are many formulations that have become “qualified” in these systems, so it’s safe to say we, as the plate developers, have had a bit of serendipity with respect to the interactions between plates and light sources. There are, however, things that we have learned about along the way that will help guide us on where to go next.
Future Developments
Future developments aren’t just “because” we can develop them; there are distinct benefits that are targeted specific to UV LED technology now that these light sources have become more readily available to test on and learn from. These benefits include:
1) Productivity…back again!
2) Optimized cure/performance
MacDermid Graphics Solutions' (MGS) Technology Strategy
Productivity and sustainability…last time - we promise!
1) Productivity…back again!
The current class of polymers in
the market today have shown distinct differences in their behavior under UV LED
conditions. Generically speaking, the “inherently flat-top dot” chemistries
cure much faster under UV LED conditions, like their behavior under bank light
conditions. With the benefits gleaned from the ability to control intensity with
said systems, in combination with the uniformity of the intensity, there is new
ability to focus on formulation speed without fear of losing control of the
plate consistency. Future iterations of UV LED products can therefore be
developed to best optimize the utilization and efficiency of these systems
without harming final quality. When combined with the automation aspect, this
has intriguing possibilities for the platemaking facilities of the future. Stay
tuned…
In addition to the monochromatic
wavelength structure of UV LED systems, the other main difference in UV LED
systems is the overall lamp intensity- i.e. it is WAY higher than typical bank
light systems. As a result, the curing
mechanism itself can radically change. This has been observed with two
main defects on the finished printing plate: inconsistent or unpredictable dot
gain, and dot cupping. While certainly
addressable via optimization of process/curing conditions, the goal of new
plate developments is to widen the platemaking window, allowing for a broader
range of optimum conditions that aren’t impacted by slight changes in graphics,
relief targets, print applications, etc…you know, the usual plethora of
conditions the industry deals with.
MacDermid Graphics Solutions' (MGS) Technology Strategy
Within the MGS development & support team, our aim is to
fully support UV LED technology as we truly believe this represents the future
pathway of flexo platemaking. The reasons for this are articulated above, but we
also feel this technology brings out the best in our photopolymer formulations, MGS is always striving for better! Similarly,
we feel we can continue to evolve our development programs to further expand
the capabilities of flexographic printing in combination with the benefits
previously outlined. To summarize, the gateway to UV LED will continue to drive
forward because of three main elements:
- The outstanding uniformity of consistency of photopolymer plates derived from UV LED platemaking, and the print benefits obtained therefrom.
- The ability to automate platemaking.
- The increasing environmental pressures that will ultimately impact mercury-based light sources that are found in the existing bank light systems on the market today.
Productivity and sustainability…last time - we promise!
It is a key plate technology strategy for MacDermid to be
prepared for this technological emergence and adoption, rather than waiting for
it happen – we don’t elevate your print by sitting on the sidelines. By working
very closely with the suppliers of UV LED technologies, our platform strategy
is focused on two key areas of strength:
- High quality formulations that exist TODAY, qualified and proven to work in UV LED systems. These include resins such as Digital RAVE and LUX ITP 60.
- Newer technology platforms that are developed to be “tuned” to UV LED light sources, providing even greater productivity and wider performance latitude than plate technologies that currently exist.
By combining our formulation expertise with outstanding
collaborative partnerships, we can help propel this technology not only to full
adoption, but to greater and greater capabilities for our industry and customer
base. Improved quality, productivity and efficiency- areas that will drive more
market share towards flexo and away from our competing technologies- while
continuing to maximize profit along the way.
To elevate your print to the next level with UV LED technology, contact MacDermid.
Based on article, “UV LED & Photopolymer Technology” by:
Ryan Vest, Global Director of Innovation - MacDermid Graphics Solutions
Ryan Vest, Global Director of Innovation, has been key in the development of industry-changing technologies such as LAVA® thermal plate processing and the LUX® Flat Top Dot technologies. He is widely known in the industry for his expertise in liquid photopolymer and corrugated plate technologies. Vest earned his Bachelor of Science in Chemistry from Berry College in 1995 and his Master of Science (M.S.) in Chemistry from North Carolina State University in 1998, joining MacDermid that very same year.
Based on article, “UV LED & Photopolymer Technology” by:
Ryan Vest, Global Director of Innovation - MacDermid Graphics Solutions
